Wing Tips
The wing tips are made of 1″ tube that is bent to shape. Fabrication of this part proved to be one of the more challenging tasks that we have been confronted with. We made a custom bending jig from wood and manually bent the tube.
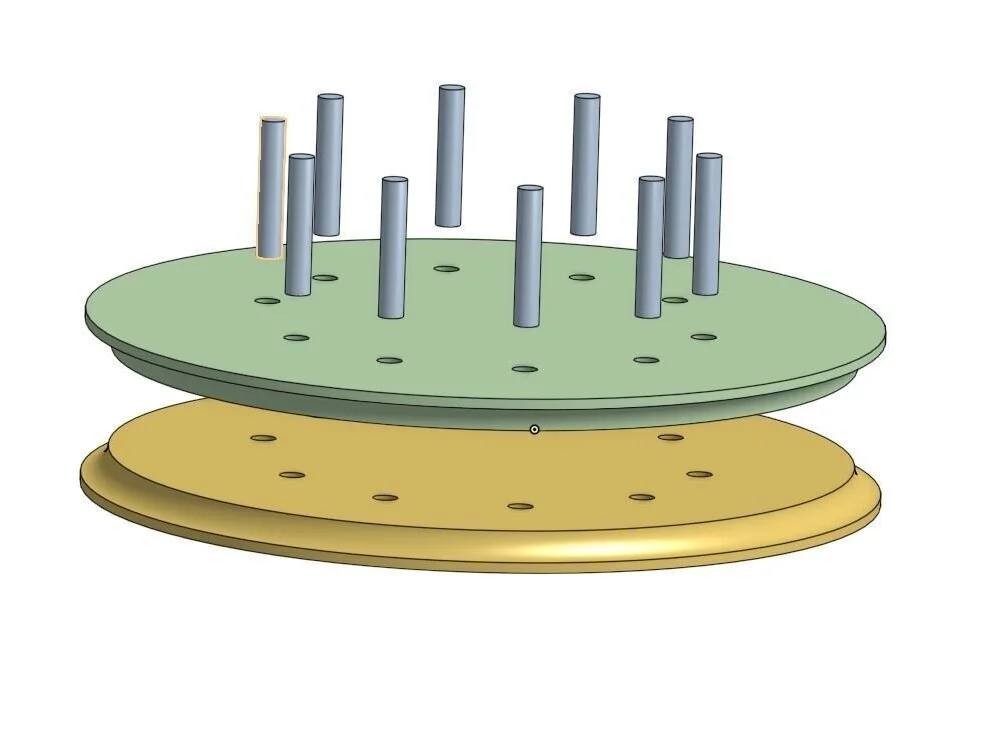
The bending jig is made from two 9-inch radius disks. Each disk is cut from 3/4" plywood and then the two halves are glued together. The dowels are used to align the disks prior to gluing.
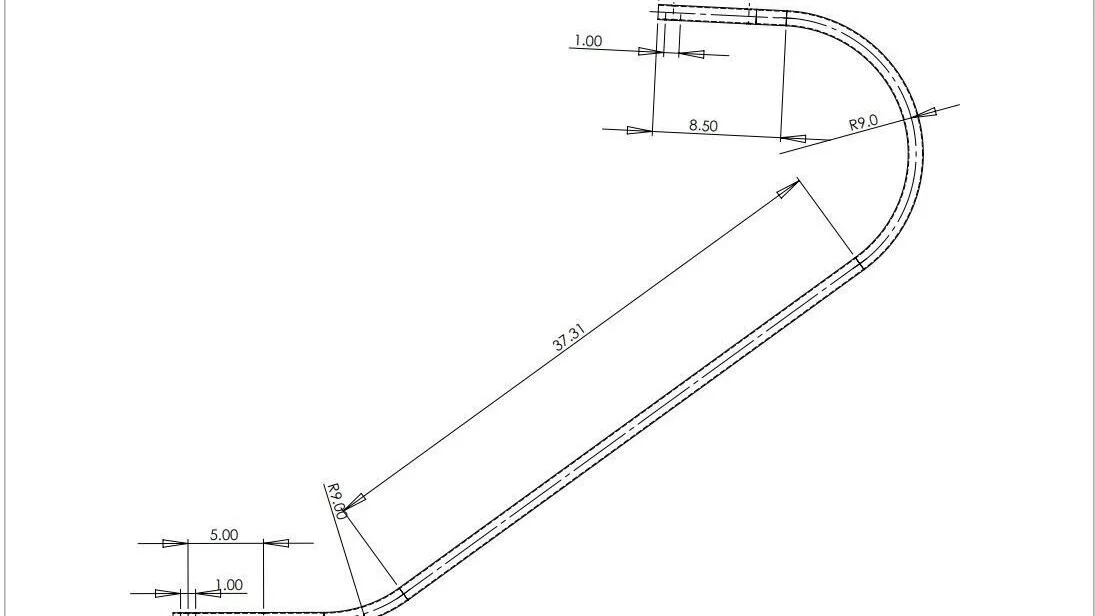
Here's the drawing of the part we need to fabricate.
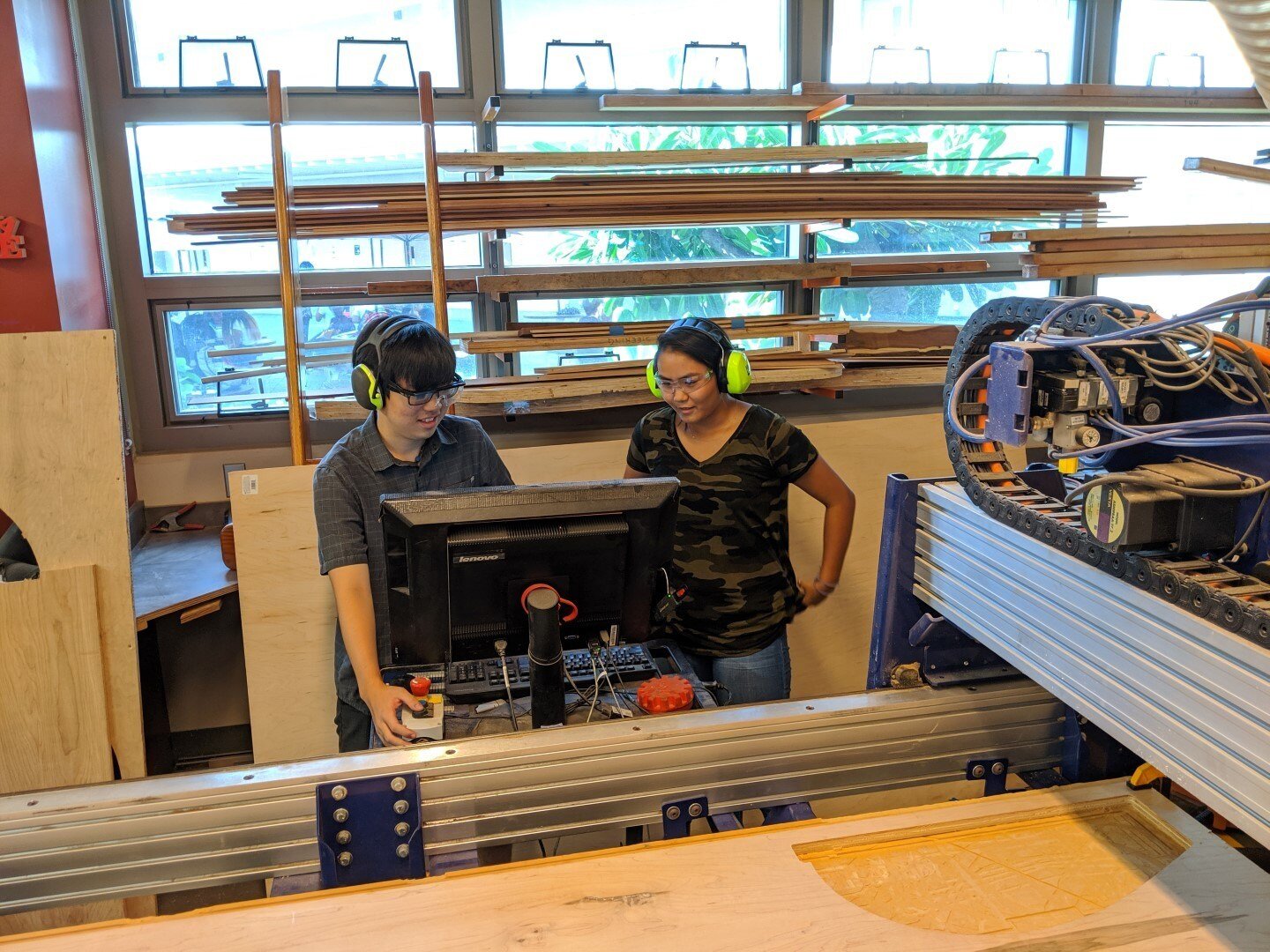
Setting up the CNC router to cut the parts for the bending jig.
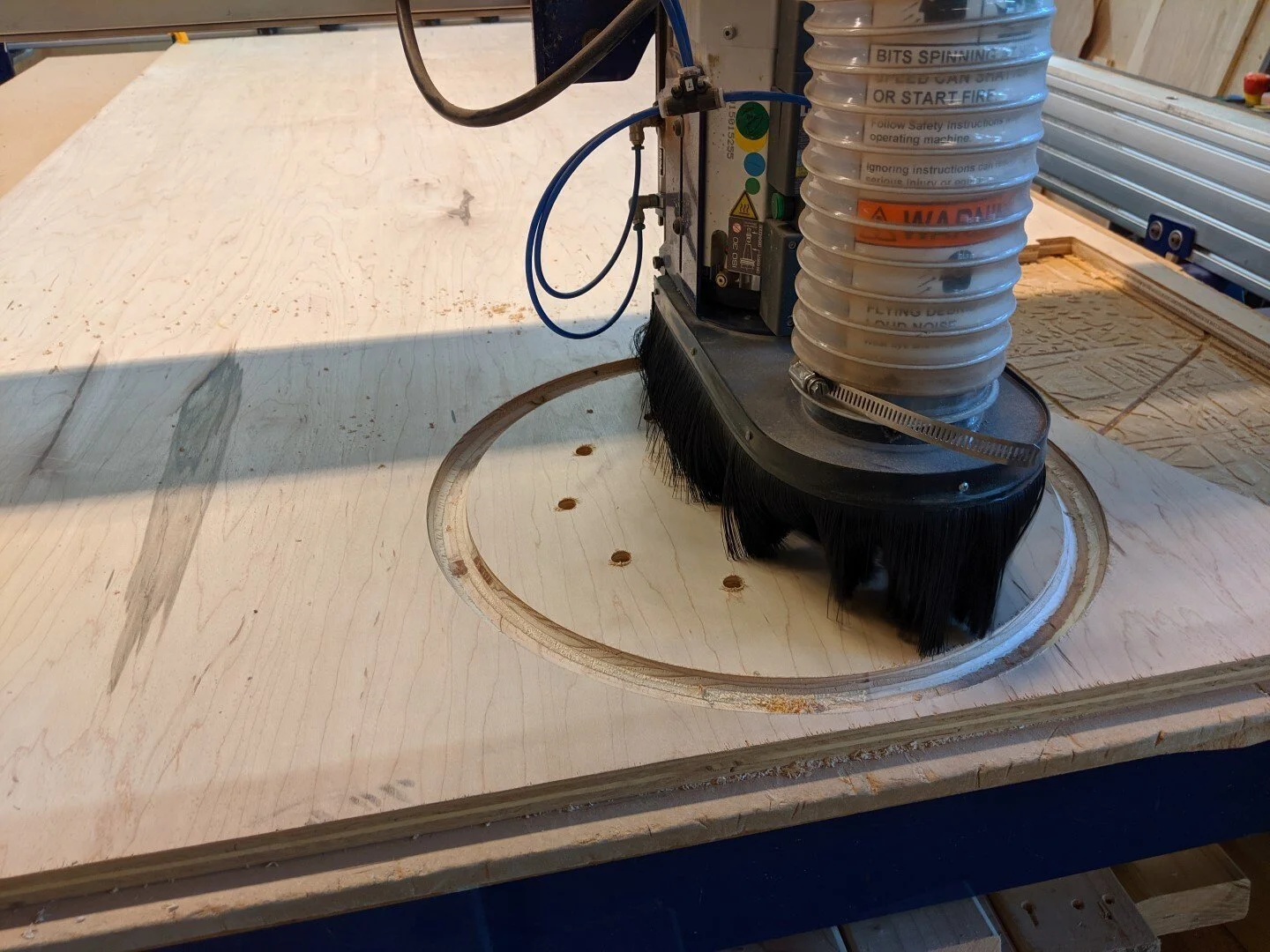
First half of the bending die is almost done.
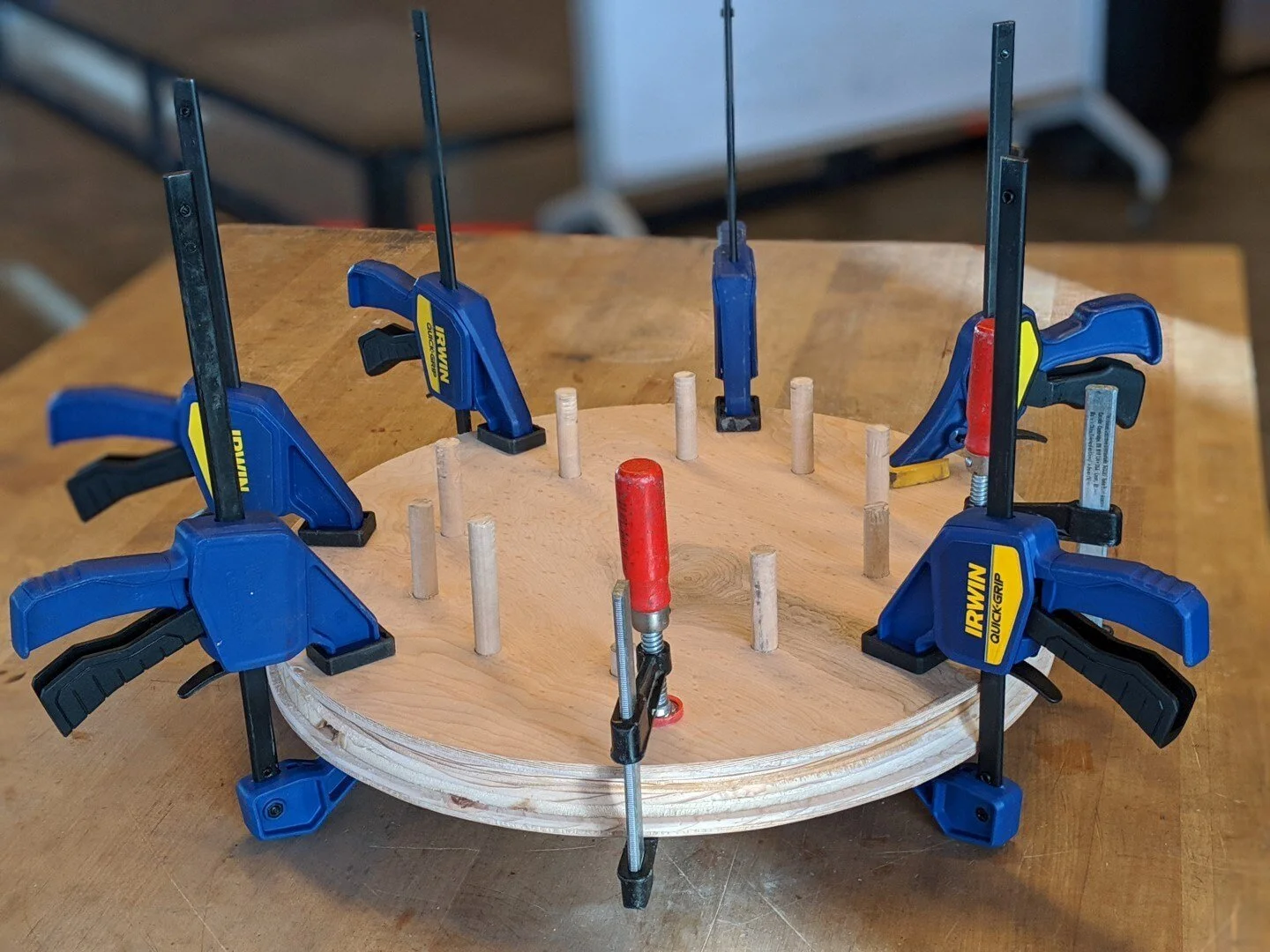
The two halves are aligned with the dowels, glued, and clamped.

The bending jig is fastened to one of our heavy work tables. We also fasented the jig we created for the keel t help clamp the tube in place. The 1" tube was filled with sand (actually the abrassive we use with our waterjet) at which time bending commenced. A fair amount of force was required to make this manual bend.

A fair bit of force was required to make the first bend of approximately 140 degrees. We had to make sure to apply the bending force as close to the die so as to not introduce any bending in what should be a straight section.
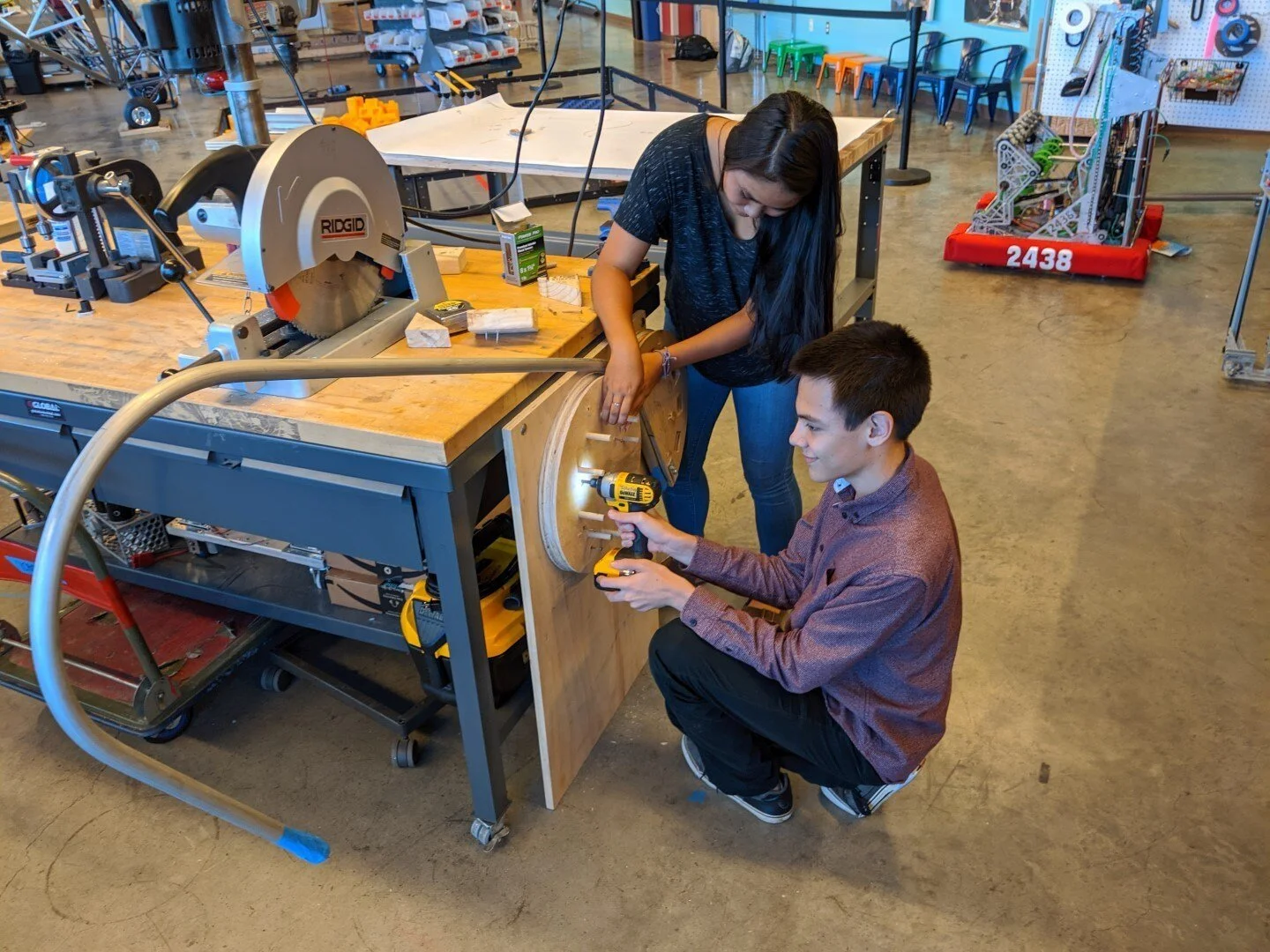
The first bend is complete. Here we are re-positioning the wing tip so that we can proceed with the second bend of about 36°.

We printed a full-scale drawing to make sure that our part was accurate. Multiple bends were made to get it just right.
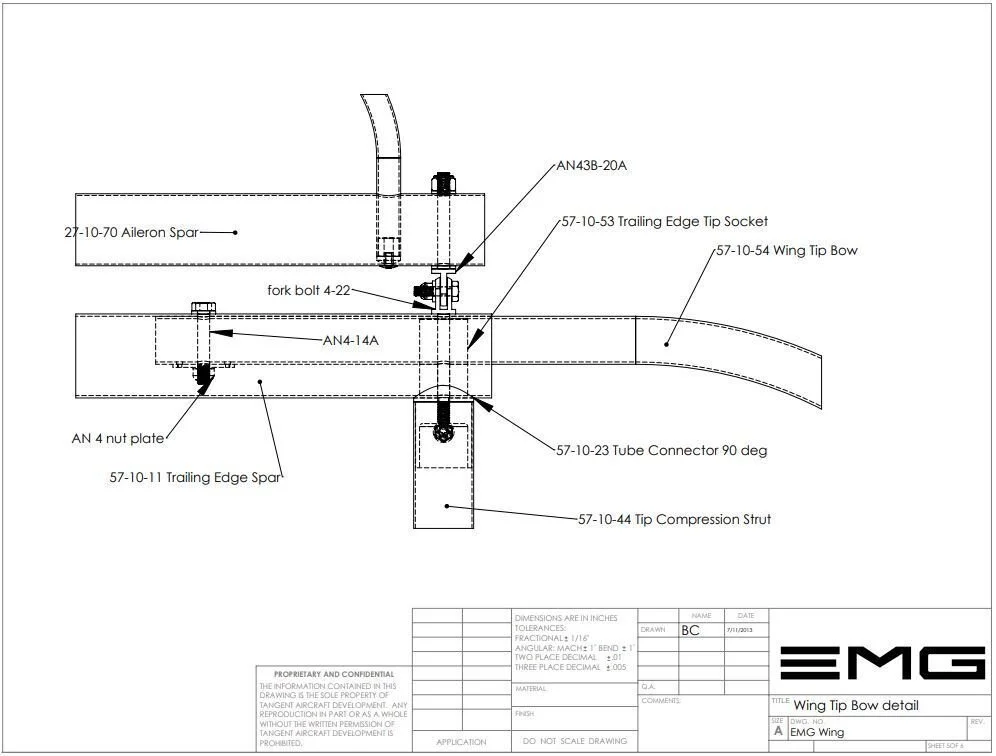
The wing tip is held in place with two bolts and a plastic socket that mates it to the larger diameter leading and trailing edges. The leading edge installation is similar to that of the trailing edge.
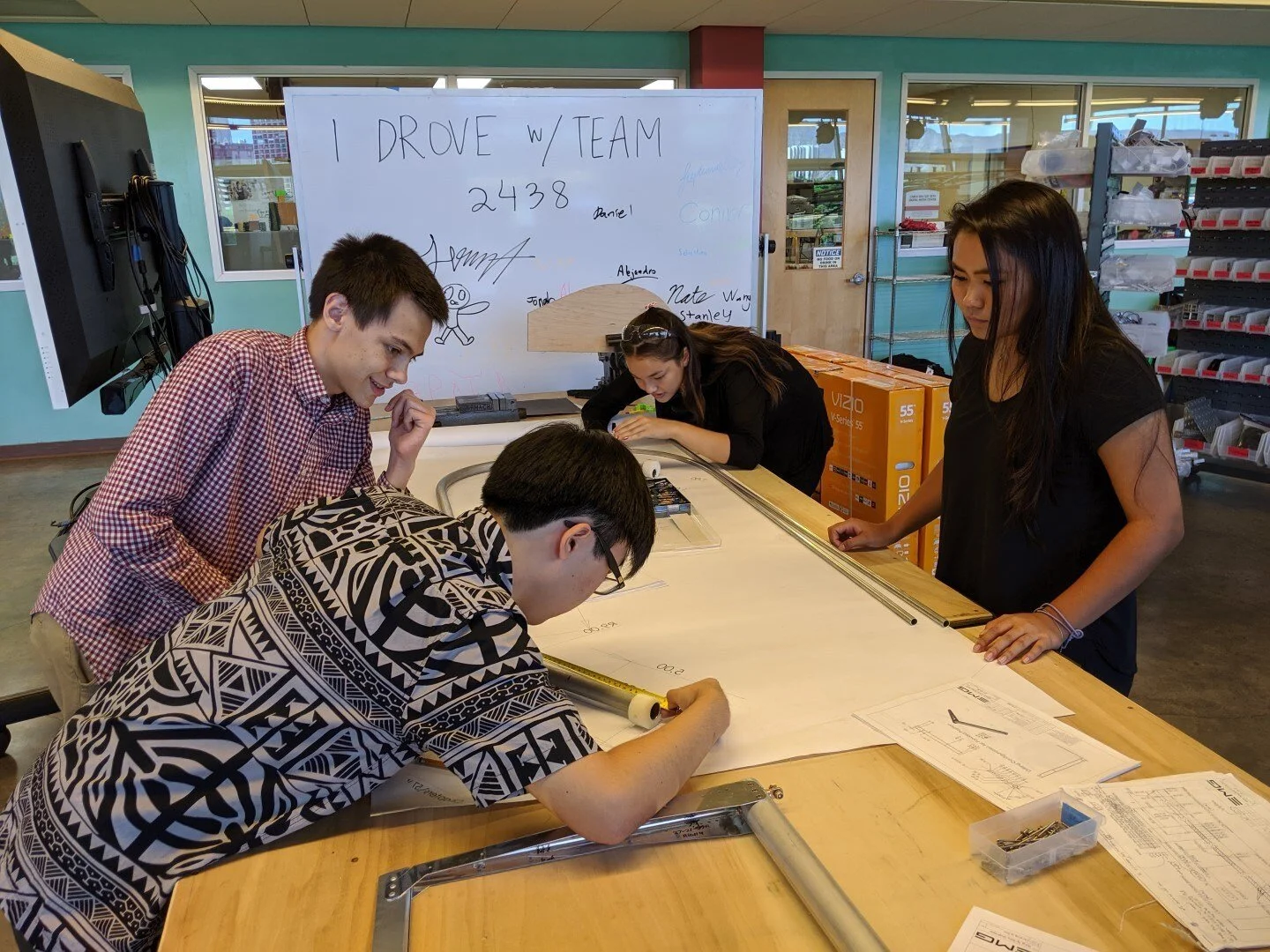
Locating the the leading edge and trailing edge tip sockets prior to installation.
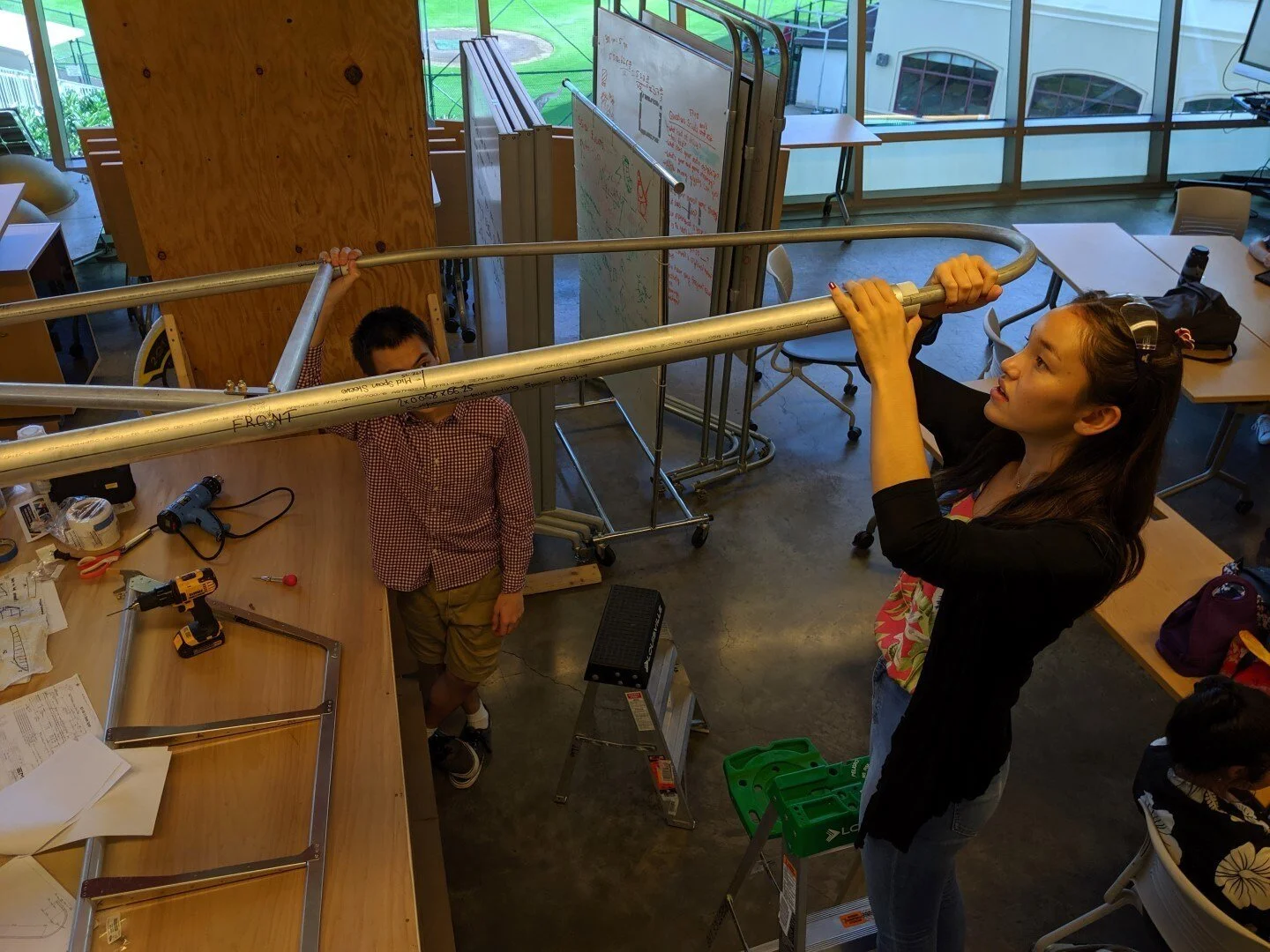
Time to install the left wing tip. A fit check was performed first, then followed by drilling the bolt holes.


The completed wing tip installed.